Garrattfan's Modelrailroading Pages
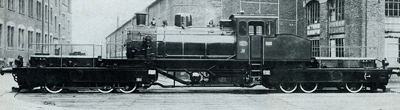
LTM 51 in HO
Het maken van de ketel
Het maken van de ketel leek niet al te moeilijk, maar ik ben geen ervaren machinewerker om het maar zo te zeggen. Eigenlijk is de ketel het grootste en moeilijkste object dat ik tot nu toe gemaakt heb. Ik heb ontdekt dat draaien en frezen allesbehlave zo simpel is als je op YouTube ziet en ik ben nog steeds zoekende in mijn leerproces. Dus het maken van de ketel werd een leerproces op zich. Maar ja zo heb ik al mijn modelbouwvaardigheden verworven: gewoon doen. Ik heb mijn weg naar een bruikbare ketel voor de LTM 51 beschreven voor de lezers die ook net beginnen met machinebewerking of dat overwegen. Voor de meer ervaren lezers zal er weining van belang zijn tenzij iemand aandrang heeft wat goed advies achter te laten of feedback te geven, . |
|
De messing buis die ik bestelde meet 22,0 mm aan de buitenzijde en heeft een wanddikte van 1,5 mm. Ik heb bewust gekozen voor een buis met een dikke wand om eventuele onrondheid in de draaibank en bij het opspannen op te kunnen vangen. De buis moet afgedraaid worden tot 21,4 mm op de rookkast (blauw), minus 0,1 mm bij de ketelbanden (geel) en nog eens minus 0,1 mm op het zuivere ketelvlak. |
|
Versie 0, een verkenning |
|
De opstelling de je hier is overigens maar een experimentje, dit werkt niet. |
Bij het maken van de ketelbrug bereikte ik het moment waarop ik de ketel wilde passen. Ik had een geschikte messing buis in bestelling maar die was nog onderweg. Dus ik probeerde mijn nog beperkte draaikunsten op een stalen buis. Dat liep niet erg goed af. Om de een of andere duistere reden wilden diverse beitels niet draaien met dit metaal. Ik bleef maar een heel ruw oppervlak krijgen.Ik moet dus maar wachten tot de messing buis komt.
|
Versie 1, raaien bij 't draaien |
|
Eerste missie is het maken van een opspandoorn om de buis überhaupt in de draaibank te kunnen inspannen. Ik vond een geschikt stuk messing (het is eigenlijk een de kraanhals van een afsluiter van de boot van mijn zwager, de afsluiter van zijn poepdoos om precies te zijn....). Na wat zagen en draaien had ik een redelijke klomp messing die min of meer bruikbaar was. Op de foto is hij nog overmaats en moet nog op maat gedraaid worden voor passing op de binnenzijde van de messing buis. Ik ben een beginnende bankwerker en ik kon de oppervlakteafwerking niet beter krijgen dan op de foto. Ik maak me er een beetje zorgen over dat dit door het verfwerk heen zichtbaar zal zijn. Niet dat de doorn onderdeel wordt van de locomotief maar als ik de oppervlakteafwerking niet beter krijg dan ga ik die ook niet krijgen op de ketel. Je kunt beter oegenen op zo'n doorn dan op de ketel zelf. |
|
![]() |
Op dezelfde dag dat ik de opspandoorn wilde gaan draaien landden twee beitels met bijbehorende wisselplaatjes op mijn deurmat, gestuurd door een vriend. Ik probeerde ze uit op de op mijn kandidaat opspandoorn, en man man, kreeg ik toch ineens een veel beter oppervlak. Bekijk de linkerzijde en oordeel zelf. Uit nieuwsgierigheid nam ik de doorn mee naar de spuitcabine en legde er een laag grondverf op. |
Het verschil is duidelijk in strijklicht. Het werk van gisteren komt door de grondverf heen, en dat van vandaag niet. Man, daar ben ik mee in mijn nopjes! |
|
Nu zette ik de zaag in de kandidaat ketelbuis. Dat is niet moeilijk als je geen lintzaag hebt. Zet een stuk of acht markeringen rondom de buis op de gewenste lengte en je zaagt een keer rond van markering naar markering. Zaag daarbij tot ongeveeer tweederde van de wanddikte. Bij de tweede slag ga je wel helemaal door het materiaal heen. Niet honder procent nauwkeurig maar je kunt de buis binnen een halve milimeter krijgen.
|
|
Ik klokte het eind van de buis in en vlakte het gezaagde uiteinde van de buis op mijn draaibank. Dit is wel een gevoelig klusje want de buis wordt alleen in de klauw gehouden ver, heel ver van de bewerking. Alleen bij lichte sneden zal de buis op zijn plek blijven zitten.
|
|
Daarna draaide ik de doorn tot de buis er nét paste op de doorn. Ook nu was de oppevlakteafwerking bemoedigend. |
|
En daar zit de ketel knus op de draaibank. De opspandoorn houdt de buis centrisch op de meedraaiende spindel rechts. Mijn meetklok zegt dat er minder dan 0,05 mm verschil zit tussen links en rechts. De uitslag van de ketel varieert wat tussen 0,15 en 0,25 mm. Niet slecht voor een beginner. Het loopt straks allemaal centrisch als het afgedraaid is, maar de ketel zal iets taps toelopen, ongeveer 0,1 mm. Als modelbouwer vind ik dat acceptabel, dat ziet geen mens. Als beginnend draaier doet het zeer, ik moet het beter kunnen dan dat. Ik leer het wel, ik leer het wel. |
|
Nou , zo goed als het nieuwe carbide beitel gisteren op de doorn werkte, zo slechts ging het op de buis. Ik geen enkele slag was goed. De beitelpunt schaatste meer over het oppervlak van dat hij er in beet. Niets hielp, snelheid verhogen, snijdiepte aanpassen, snijhoek. Ik worstelde bij elke slag. Dus zocht ik mijn toevlucht bij HSS en zeker, de afwerking verbeterde wel (linkerzijde van de ketel) maar ontstond er een soort vibratie die een golfvorm in het oppervlak van de ketel maakte. Die kreeg ik er maar niet uit. |
|
Links met de HSS-beitel, uiterst rechts een restantje van de beitel met wisselplaatje. |
Een close-up van de golfvorm die achterbleef bij de HSS-beitel. |
Na veel experimeteren kreeg ik de inval dat de opspandoorn en trok de spindel zo strak aan als ik kon. Vvanaf moment was het resultaat superglad (linkerhelft van de ketel), zo glad dat zelfs de vingernageltest slaagde: met je vingernagel over het snijvlak gaan en dan niets voelen of horen krassen. Vervolgens draaide ik het golfpatroon er uit. Eindelijk had ik een ketel met een net oppervlak. |
|
Tegen de tijd dat ik een redelijk resultaat kreeg had ik zoveel slagen gemaakt dat de ketel uiteindelijk ondermaats was geworden. Dus daarna was de ketel afgeschreven. Omdat dat toch het geval was oefende ik er nog wat dingen op, in het bijzonder het snijden van de ketelbanden. |
|
Versie 2, het geleerde in de praktijk brengen.Ik zaagde een tweede stuk van mijn messing buis. Gelukkig had ik een stuk van 25 cm besteld zodat ik genoeg materiaal voor drie pogingen in voorraad had. Ik kon nu de verzamelde ervaring te gelde maken:
|
|
De tweede poging ging redelijk goed. Zelfs het maken van de ketelbanden ging makkelijk. |
|
Toen de ketelbanden er netjes opzaten, sneed ik de ketel aan bij de klauwplaat om hem af te snijden. Dat deed ik maar deels. Ik zaagde hem daarna gewoon af. Dat bleek een grote fout, zoals nog zal blijken. Met de vijl werd de achterzijde van de ketel opgeschoond van de zaagresten. |
|
Wauw! De volgende taak was om de opspandoorn eruit te halen. Ik stookte de ketel op met een gasbrander, maar tot mijn afgrijzen gaf de doorn geen krimp. Wat ik ook deed, er zat geen beweging in. En nu kwam mijn fout aan het licht. Nu het opspangedeelte van de ketel was gezaagd kon ik hem nergens beetpakken zonder hem te beschadigen. Bovendien was hij nog gloeiend heet ook. Ik probeerde het ongeveer een uur. Toen kwam ik tot de slotsom dat ik iets anders moest verzinnen. |
|
Ik ging de mechanische kant op: de doorn van binnenuit wegwerken tot er weinig van over was en dan als nog de restjes er uit stoken. Daar was ik de rest van de dag mee bezig. Eerste een flink gat boren en dan met de frees sleuven maken in de richting van de wand. Alles heel voorzichtig omdat ik de ketel niet kon inspannen. Toen ik eenmaal zover was als op de foto, kon ik hem heet stoken en de vier stukken vielen er een voor een uit. |
|
Maar eerlijk is eerlijk, het is een schoonheid, toch? Ik was erg trots op het resultaat. Het oppervlak dat je ziet komt zo uit de draaibank, er is geen schuurpapier aan te pas gekomen. Sterker nog, de wat doffe kant van de rookkast rechts, is ontstaan door schuren met 1200 schuurpapier!
|
|
Even controleren aan de hand van voorzijde van het machinistenhuis. |
Wat? |
Ja, de volgende dag bracht ik ketel en machinistenhuis samen en ontdekte dat de ketel te klein was. Serieus te klein want op de foto boven staat hij op zijn rookkast. De vuurkist is nog eens 0,2 mm smaller.
Ik moet een fout gemaakt hebben bij het opmeten van de tekening, hoewel ik me herinner dat ik het zeker twee keer gemeten heb. De ketel was meer dan 1,5 mm te klein. Ik overwoog om het te verbergen. Wie zou het zien? Wie zou het weten, behalve ik zelf? Ik zou het gat tussen de ketel en het machinistenhuis moeten vullen.... Maar nee, uiteindelijk kon ik dat niet accepteren. Dus ketel nummer twee is ook schroot. Ik liet de kwestie een paar dagen rusten om over mijn teleurrstelling heen te komen.
|
|
Dit is waar ik nu stond
|
|
Versie 3, eindelijk succes.Bij poging twee was mijn opspandoorn verloren gegaan, daar moest ik dus een nieuwe voor maken. Ik had geen geschikt restje messing meer, dus die moest uit de nieuwe voorraad gedraaid worden. Tegelijk wilde ik ook de rookkastdeur maken. Ik besloot die te combineren om het materiaalverlies tot een minimum te beperken. Dus ik toog aan het werk om een "draaiplan" te maken voor beide. |
|
Dit was het plan. De gesteepte lijnen geven de diameter aan van het ruwe materiaal van 20 massief messing uit mijn voorraad.
|
|
Alles klaar voor een derde poging. Het ruwe materiaaal is al vlak gedraaid en de eerste slagen zijn gemaakt om de kleine verhogingen te maken die midden op de rookkastdeur zitten rond ht handwiel. Ik gebruik hier een ander HSS gereedschap met een relatief scherpe punt (75 graden) en een vlakke bovenzijde. De punt heeft een kleine radius om een gladder oppervlak te krijgen.
|
|
Overal spanen! Het goede nieuws is echter dat de vlakke bovenzijde van de HSS beitel de spanen netjes breekt. |
|
Toen ik eenmaal bij het voorvlak van de opspandoorn was aangekomen pakte ik mijn vijlen en gaf de roookastdeur de gewenste kromming. Af en toe controleerde ik die met een uit papier gesneden sjabloon. Het zal slechts een benadering zijn, maar als het er goed uit ziet dan zal het wel ongeveer kloppen. Daarna stak ik de deur af met de metaalzaag. |
|
Toen de deur klaar was stond ik voor een dilemma. Wat moest ik doen nadat de ketel op maat gedraaid was en de opspandoorn verwijderd:
Dat lijkt van weinig belang, maar schijn bedriegt.
This seems of little consequence but sure enough there is. De laatste methode is de meest nauwkeurig en zal minste problemen geven met het solderen.maar het is ook de meest riskante werkwijze omdat de ketel zo ver uit de klauwplaat steekt om de binnenzijde te draaien. |
|
Ik realiseerde me ineens dat ik de voorplaat aan de rookkast kon solderen VOOR het draaien van de ketel en dat ik het dan als alternatief kon gebruiken voor de opspandoorn. Ik zaagde dus een plaat van 0,75 mm messing en soldeerde die met 240C soldeer aan de toekomstige rookkastzijde en draaide af tot ik bijna aan de buitenzijde van de messing buis kwam. Daarna mat ik de centriciteit van de ketel in, boorde een centergat, en daar had in mijn opspandoorn!
|
|
Nu draaide ik de ketel tot 21,4 mm voor de rookkast Het oppervlak was niet zo mooi als ik had gehoopt, maar een beetje schuren met 320, 800 en 1200 schuurpapier kwam het goed.
|
|
Daarna deed ik een slag met 0,05 diepte om op het vlak van de ketelringen te komen, and nog eens in drie stappen een korte salg van 0,05 mm om de ringen uit te draaien en op de zuivere ketel te komen. |
|
Ik wilde de installatie van de ketel niet in gevaar brengen door de voorzijde met zware boren te gaan bestoken met het risico dat ze in de relatief dunne plaat zouden grijpen. Ik paste dus het voorbeitel toe die ik had gemaakt voor de taatsen. Ik vrat daarmee voorzichtig de voorzijde van de plaat weg vanuit het midden tot vlakbij de rand. Toen de plaat "door" was sneed ik van binnenuit naar buiten. Toen ik eenmaal op de uitgezette lijn kwam paste de deur er strak in. |
|
Het bewijs van alle dingen is de passing op de voorzijde van het machinistenhuis. Eindelijk succes! | |
Nou, dat is toch een plaatje om van de genieten! |
|
De ketelbanden van dichtbij | |
Alle drie versies |
|
De ketel knus op de ketelbrug |
|
Daarna kon ik beginnen met het uitrusten van de ketel | |
Sign my
GuestBook